Baffinland Iron Mines
Introduction
The Milne Inlet Port Facility, located in the far north arctic region of Nunavut, Canada. Operations consists of a manual stockyard and reclaim circuit feeding a reclaim conveyor and two slewing, shuttling shiploaders, sited on a single berth, land backed wharf. Erected in 2015 as a turn-key design the 3.5Mtpa shiploading circuit only managed to export 0.9 Mt of iron ore during that year.
The Port is ice bound for most of the year and therefore requires all shiploading operations to occur over a 90-day period from the middle of summer to the middle of Autumn. Given the heavily restricted operational window, the availability requirements for the shiploading circuit are exceedingly high over this short period.
From 2015 Andvare have been engaged by Baffinland Iron Mines (BIM, the Company) to assist with the modification of the materials handling systems in the reclaim and shiploading circuits at BIM’s Milne Inlet Port Facility. The team at Andvare have since completed multiple upgrade packages boosting the export quantity from the initial 0.9 Mt in 2015 to 5.86 Mt in 2019, a 650% increase.
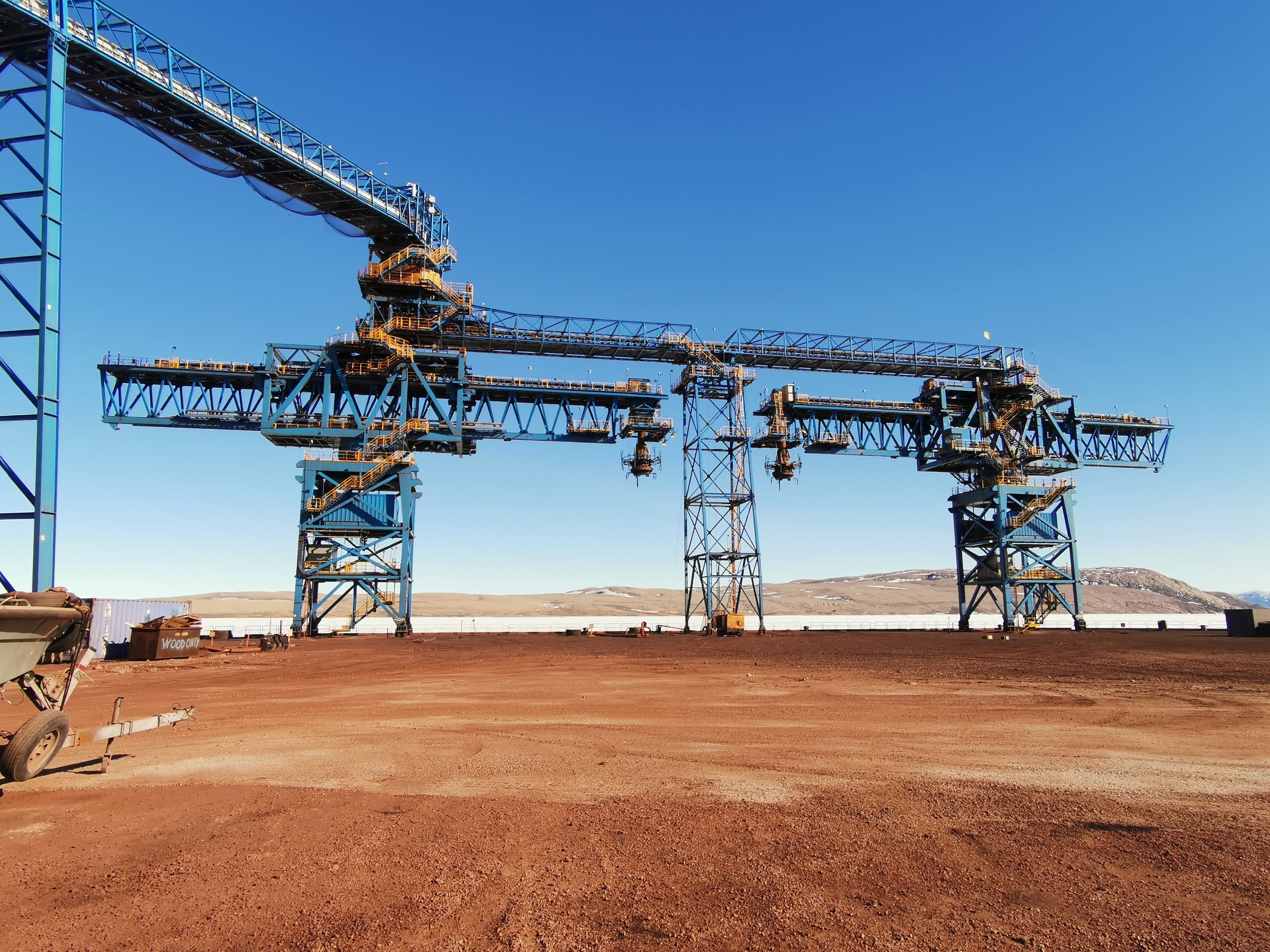
Issues
During the initial load commissioning, it was identified that the shiploading circuit does not meet the expected performance requirements, instead, the shiploader revealed the magnitude of work needed in order to satisfy the promised capabilities of the machine. Over the 5 years of involvement, Andvare have identified numerous design issues, the following having the greatest impact on shiploading reliability and capacity:
- Wear liner material not able to withstand abrasive characteristics of the ore;
- Frequent chute blowouts;
- Frequent chute blockages (especially fines);
- Poor belt tracking;
- Belt cleaning system ineffective;
- Product quality degradation from poor flow trajectory and high energy impact.
Solution
Andvare typically provide BIM with a complete annual upgrade package to suit the available budget for the year. We undertook the works from initial concept to final installation and commissioning. Over the past 5 years, Andvare was able to increase the efficiency and performance of the shiploading circuit by addressing critical design flaws, as well as focusing on preventative maintenance and reducing maintenance downtime.
Andvare’s engineering team have significantly reduced blocked chute events by redesigning most of the transfer chutes in order to slow down material flow, control its trajectory and eliminate potential bottlenecking. The original wear plates have been mostly replaced with ceramics, dramatically outperforming its predecessor, with most chute liners surviving a whole shipping season before the need to be replaced. All head chutes have also been fitted with an adjustable deflector plates, providing the ability to adjust the impact location downstream.
Downtime during wear liner changeouts has been reduced by integrating a quick changeout system for high wear areas such as the loading zones. An innovative rail system allows the load boot to roll in and out of the operating position with the ability to be swapped with a pre-lined load boot in a matter of minutes.
BIM are now at a stage where the capabilities of the shiploader exceed the output capacity of the mine, with 2019 being the first year that the exported tonnage exceeded the mines output, where the mine had produced 5.7 Mt of ore with 5.86 Mt shipped. Andvare now provide BIM with an annual spares package which accounts for consumables during the shipping season, chute liners and general wear areas now lasting at least 6Mt compared to 50kt previously experienced during 2016.
Andvare design and innovation has made this possible.
Benefits
- Significant increase in shiploader capacity.
- Reduced maintenance requirements.
- Boosted reliability of shiploading circuit.
- Boosted efficiency of shiploading circuit.